The Anode , as an electrode or positive pole in aluminium production process and in Electrolytic Cells has the task of transmitting of electrical current and combining with existing oxygen in aluminium oxide. Anodes for electrolytic cells and carbon materials for pots lining have been provided in (Carbon Plant) and anode making workshops. This workshop is consisted of anode making , baking and rodding room .
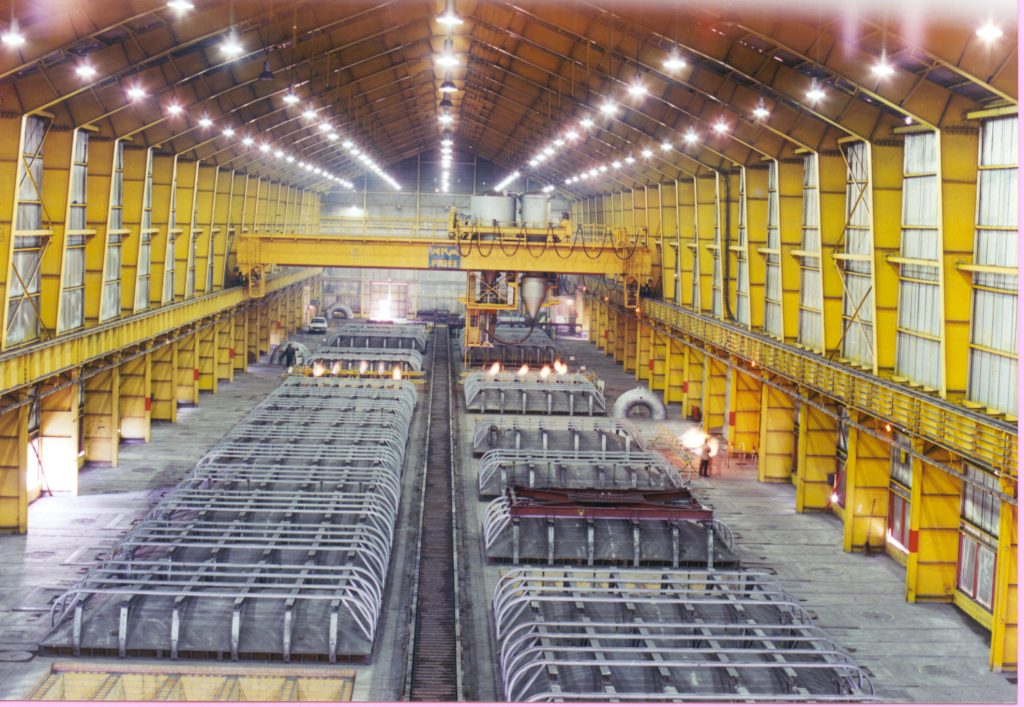
Baking Room(closed)
1.Anode Making Workshop (Green Mill)
The raw materials include (Coke, H.S.P bitumen and baths back ) are used for making of raw anodes (Green Mill) after controlling the amount of materials, granulation and mixing them by mixer, then the prepared past for pressing and converting into cubic block 40*52*40 cm 3 by conveyor is sent to press machines. The average approximate mixing time in blenders 55-70 minutes and the temperature of the HTM oil is 220-240 o c and the temperature of the output ,green paste from the mixer is about 150 o c.
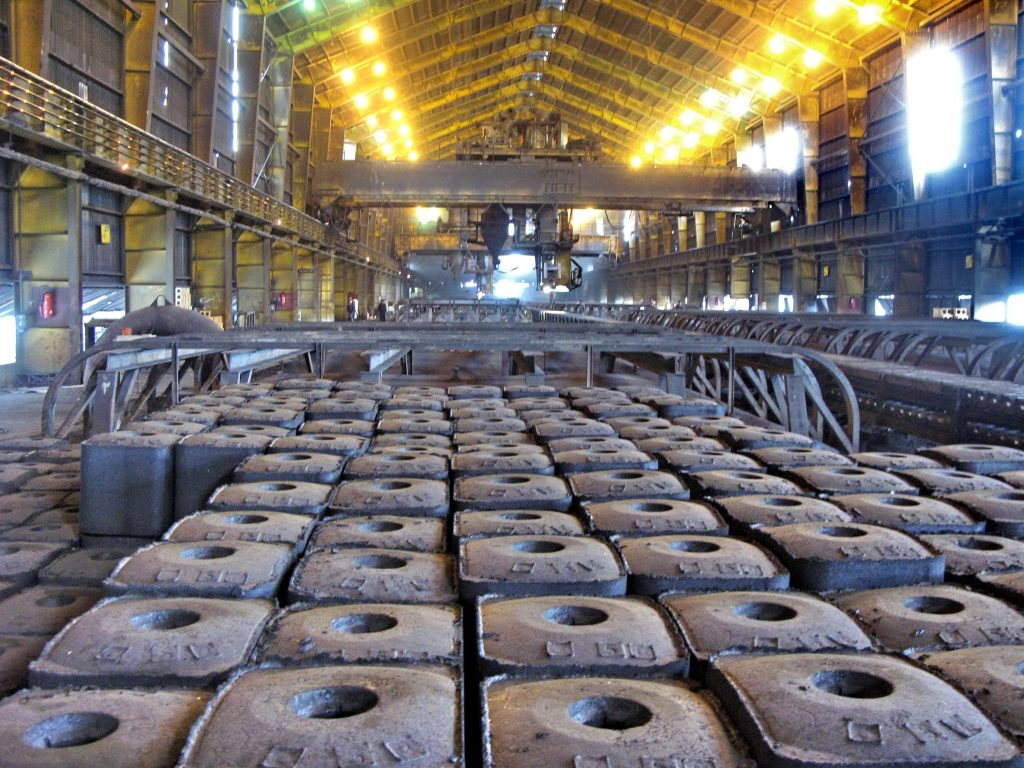
Baking Room
2. Anode Baking Workshop
This workshop include two baking parts (open and closed). In order to increase the electrical conductivity of the anodes, these anodes are sent to the anode baking workshops. This workshop consists of two sections, the old baking (open) and the new one (closed). Anode baking process takes time 22 to 23 days, which is heated in thermal process of 1250 oc, then they cool off at ambient temperature.
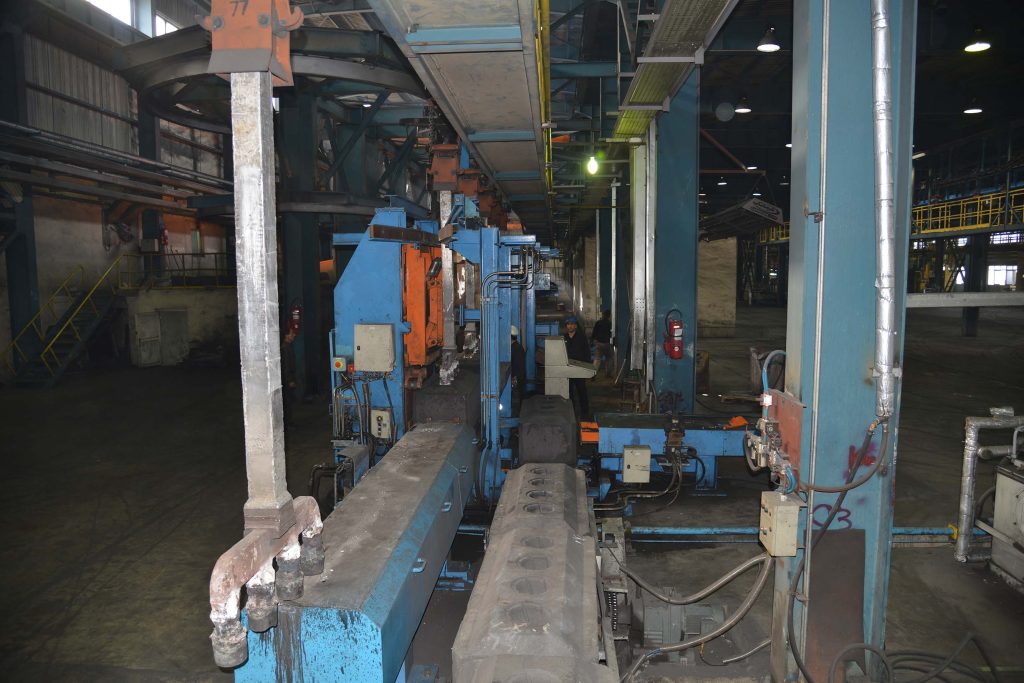
Rodding Room
Open Anode Baking Workshop:
In this workshop there are sixty sections which each section has 5 pits and each pit has a capacity of 140 to 154 anode blocks, and anode baking process will be performed automatically.
Closed Anode Baking Workshop:
In this workshop there are sixty sections which each consists of 5 pits. The anodes are arranged in 6 rows of 12 lines in each pit. The temperature of the pits is measured by the thermometer.
Anode Making Workshop of 200 KA Lines:
This workshop will be established for the provision of new pot room anode in the size of 60*80*150 cm 3 with advanced technology having a safety certificate and equipped with pollution control system from accredited (valid) European companies outside smelter and Arak city.All documents, commitment of Iranian aluminium company according to environmental and safety regulations are presented to the relevant organizations such as environmental organization.
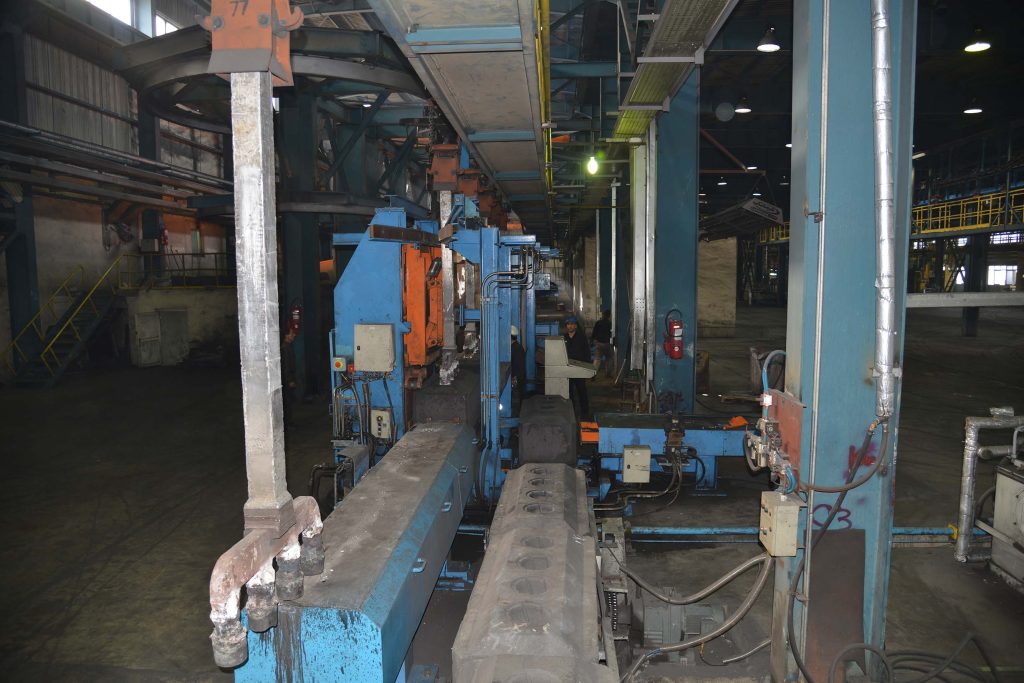
Rodding room for 200 KA reduction cells

pouring the melting gray iron around the stub
Rodding Room:
In this workshop, the baked anodes are connected by placing steel stub in the cavities of the anode and pouring the melting gray iron around the stub, connecting the steel stub and aluminium rod to the carbon anode ,then the prepared anode is sent to the pot room workshop which acts as positive ion tn reduction cells..